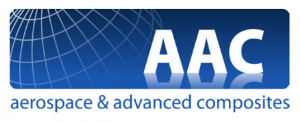
Address
Aerospace & Advanced Composites GmbH
Viktor-Kaplan-Straße 2
2700 Wiener Neustadt
Austria
Website
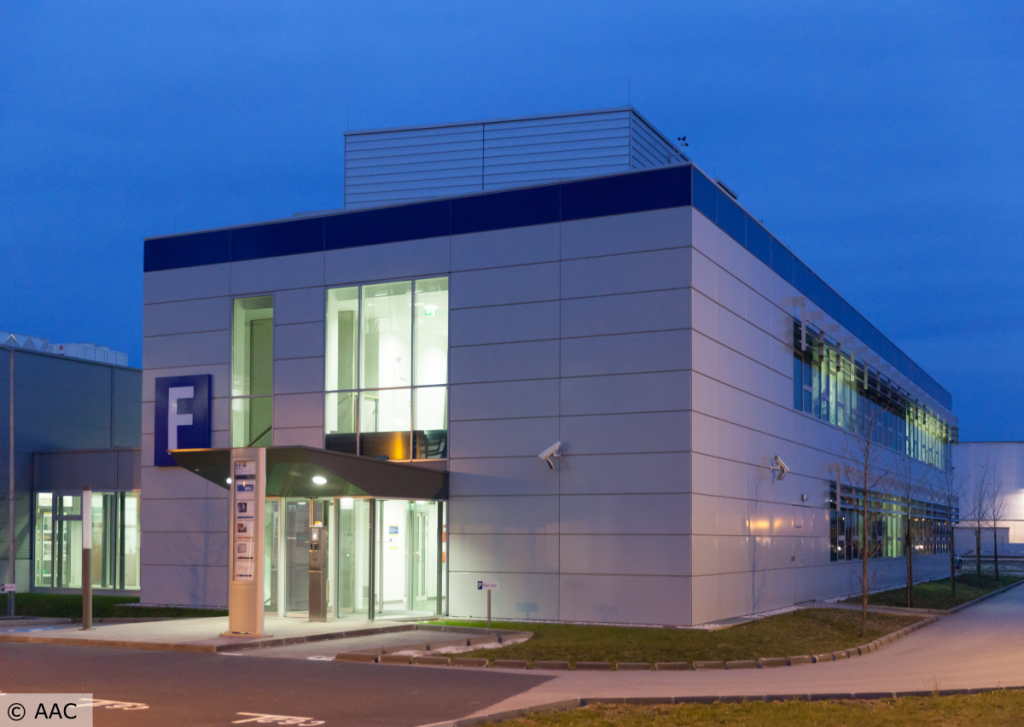
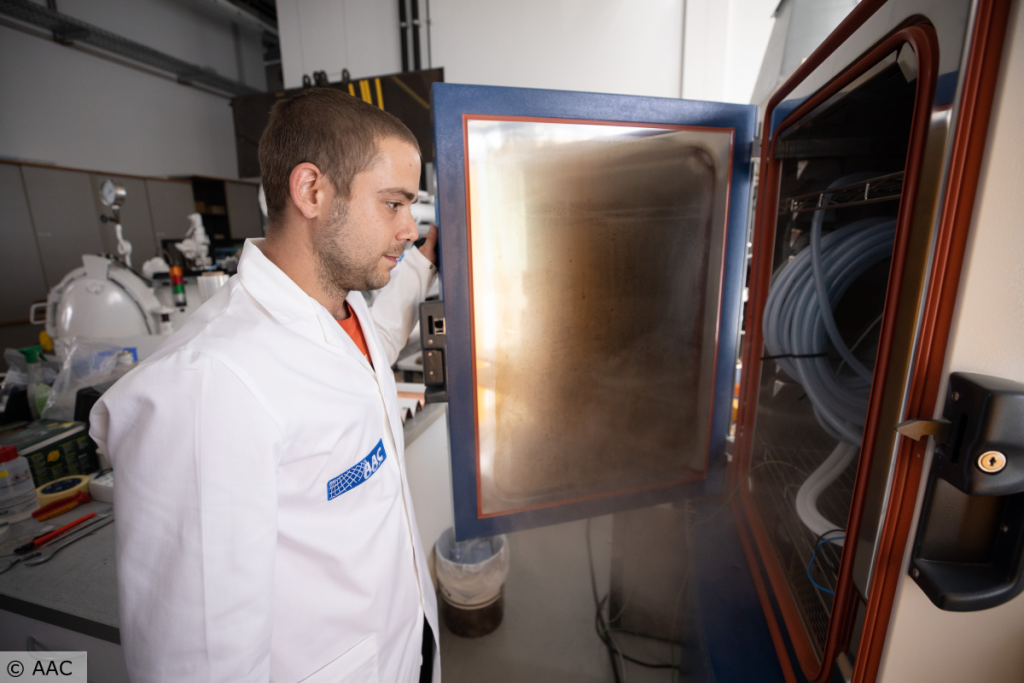
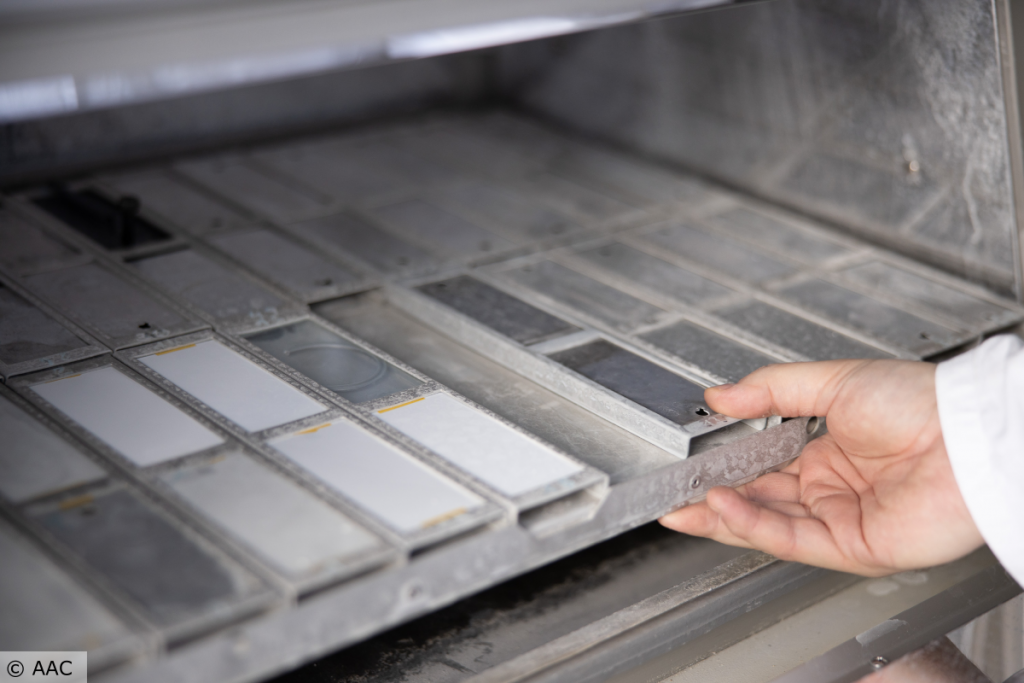
Aerospace & Advanced Composites GmbH
The Aerospace & Advanced Composites GmbH (AAC) was founded in 2010 and is a subsidiary of the AC2T, the Austrian Excellence Center for Tribology. AAC specifically acts as a service provider in the field of application-oriented research and technology development, combining a broad interdisciplinary catalogue of skills with specialized know-how. AAC is a coordinator of European and national research cooperation projects and networks in aeronautics and space and is in close cooperation with the association of the European aerospace research institutions. AAC has 25 employees comprising an interdisciplinary background in physics, chemistry, materials science, polymer engineering and mechanical and electrical engineering. More than one hundred research projects have been successfully concluded in the past 20 years.
AAC offers a wide spectrum of test facilities for materials development and characterization of high standard, some of them regarded as rare and in specific aspects unique. The AAC specializations are in the following fields:
- AAC has been involved in R&D of anti-ice coatings since 10 years and has successfully participated in 7 (two currently ongoing) national projects, involving wind park operators (WEB) and aircraft manufacturers (Diamond Aircraft).
- AAC has developed a conductive coating material for heating of aircraft or windmill leading edges and is in the process of commercialization.
Role in the project
In the project AAC will work in the field of passive anti-icing (pagophobic) coatings and electrothermal de-icing systems. Both coating types are developed and formulated at AAC.
- Definition of test procedures in view of certification for adhesion, cohesion, durability and reliability tests of icephobic / superhydrophobic surfaces
- Pariticipation in the layout and design, as well as the adaptation and assembly of the hybrid IPS for wings
- Testing of the hybrid IPS in relevant conditions